Large reservoir mixing: CFD-based improvement (Netherlands)
Optimal design of inlet and aeration in drinking water basin using computational fluid dynamics (CFD) modelling. Aeration was taken into account. Multiphase CFD simulation of air and water. Shortcircuiting and dead zones avoided. Optimal hydraulic reside
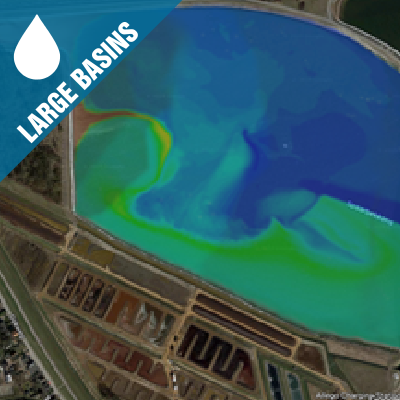
Poor mixing in large water intake and storage basins can cause algal blooms and operational problems due to water quality peaks entering the treatment. While dead zones and shortcircuiting should be avoided, we have observed poor mixing in all of the large basins we have simulated so far.
- Decisions with regard to operation (flow rates),basin geometry, aeration or inlet/outlet configuration are extremely critical. Optimal basin design without using CFD is nearly impossible.
- This case example shows how we conducted a full CFD analysis and improvement testing in a few weeks.
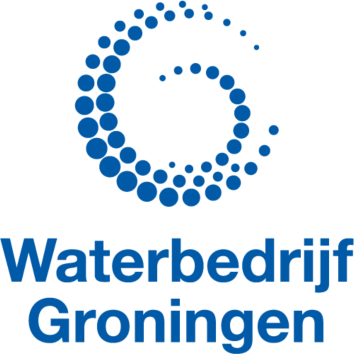
The Dutch drinking water company Waterbedrijf Groningen, produces drinking water from surface water and ground water. The surface water treatment side includes a large mixing basin that serves the following purposes:
- Peak shaving (you don't want canal water fluctuations to directly impact treatment)
- Natural purification (impact of sun and biological conversions during the time in the basin)
The following questions were answered:
- How efficient is the mixing in the basin? (the basin was designed without the help of CFD),what are the major flow patterns, and how can we potentially optimize the mixing?
- What is the impact of the aeration (2 aerators installed),and are they optimally located and operated (e.g. air flow rates)
- Where is the optimal sampling location (or sometimes chemical dosing location?)
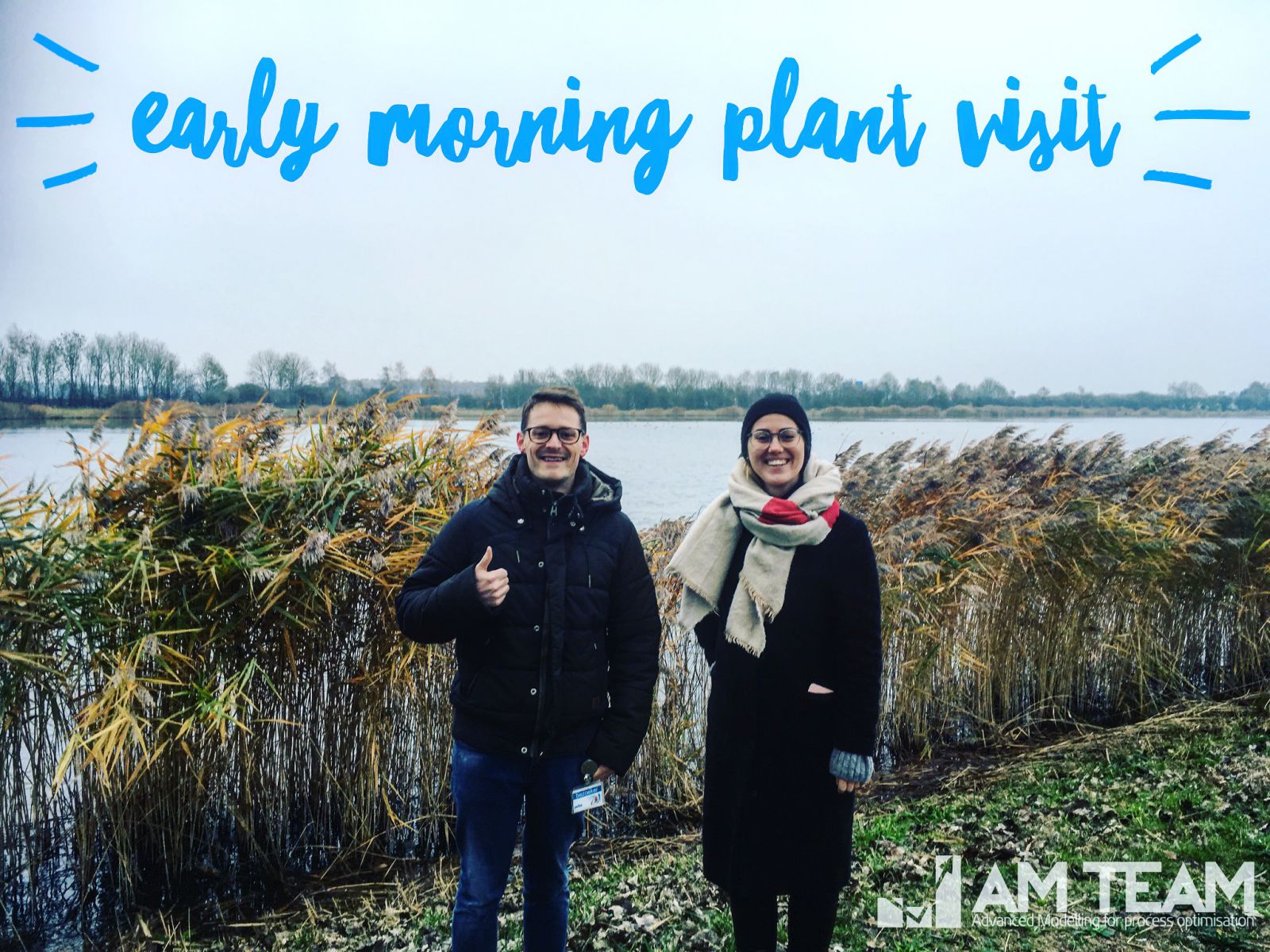
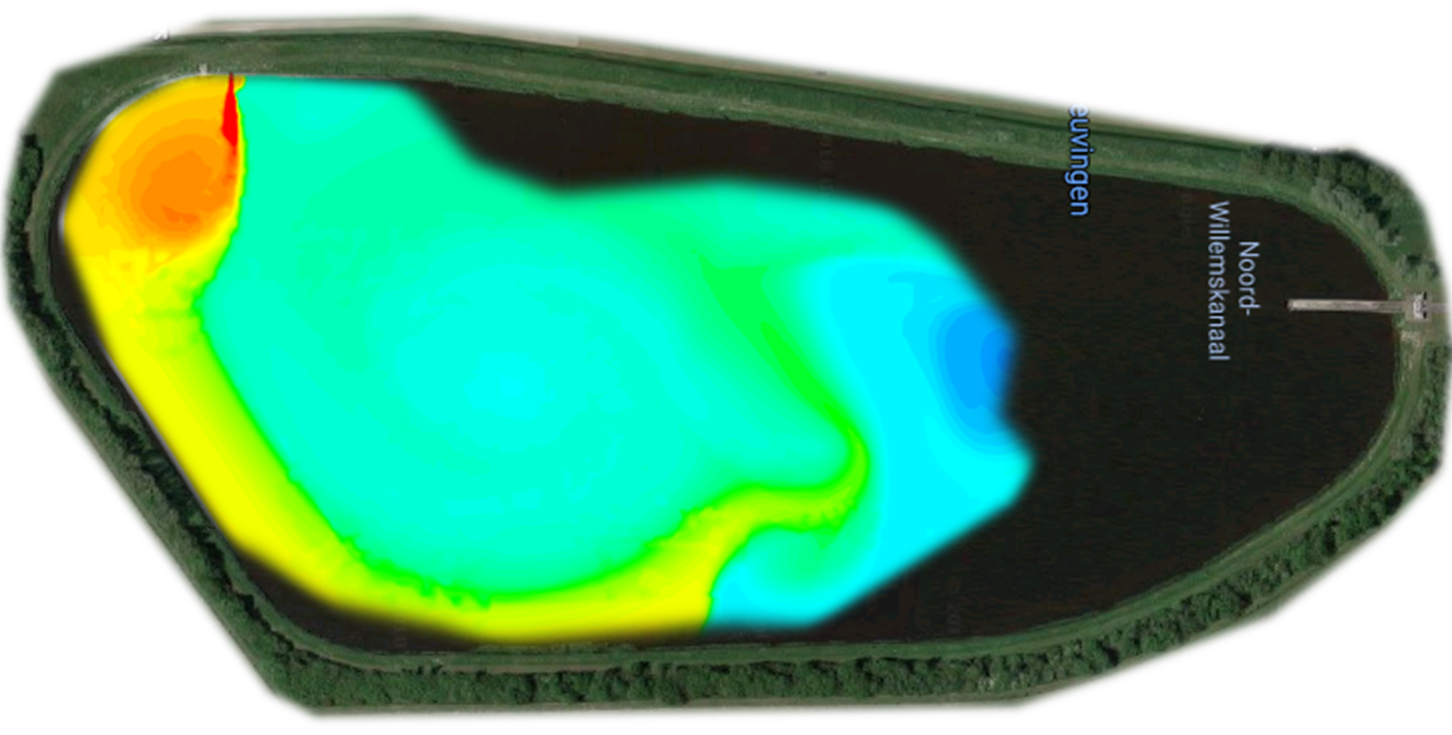
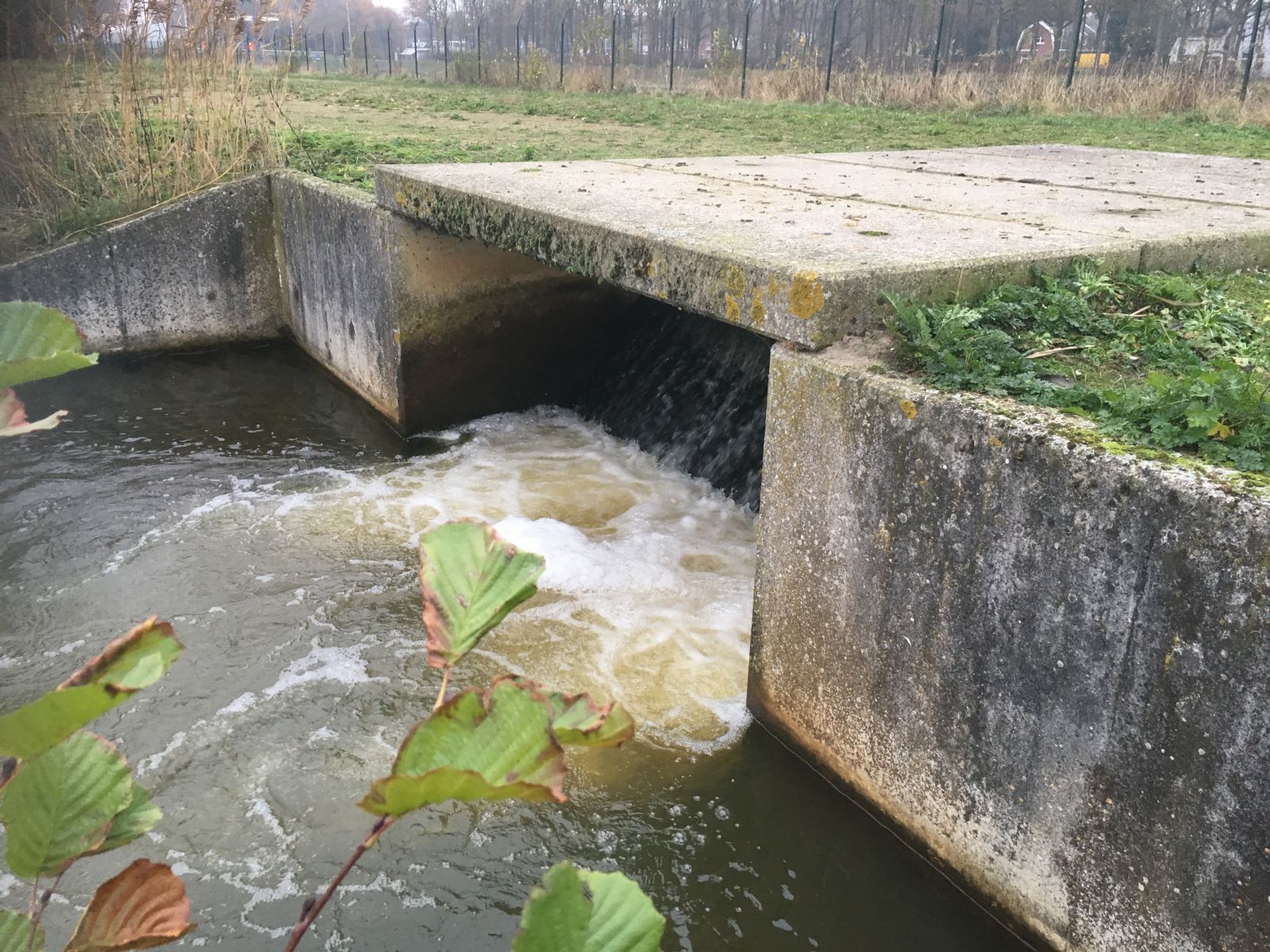
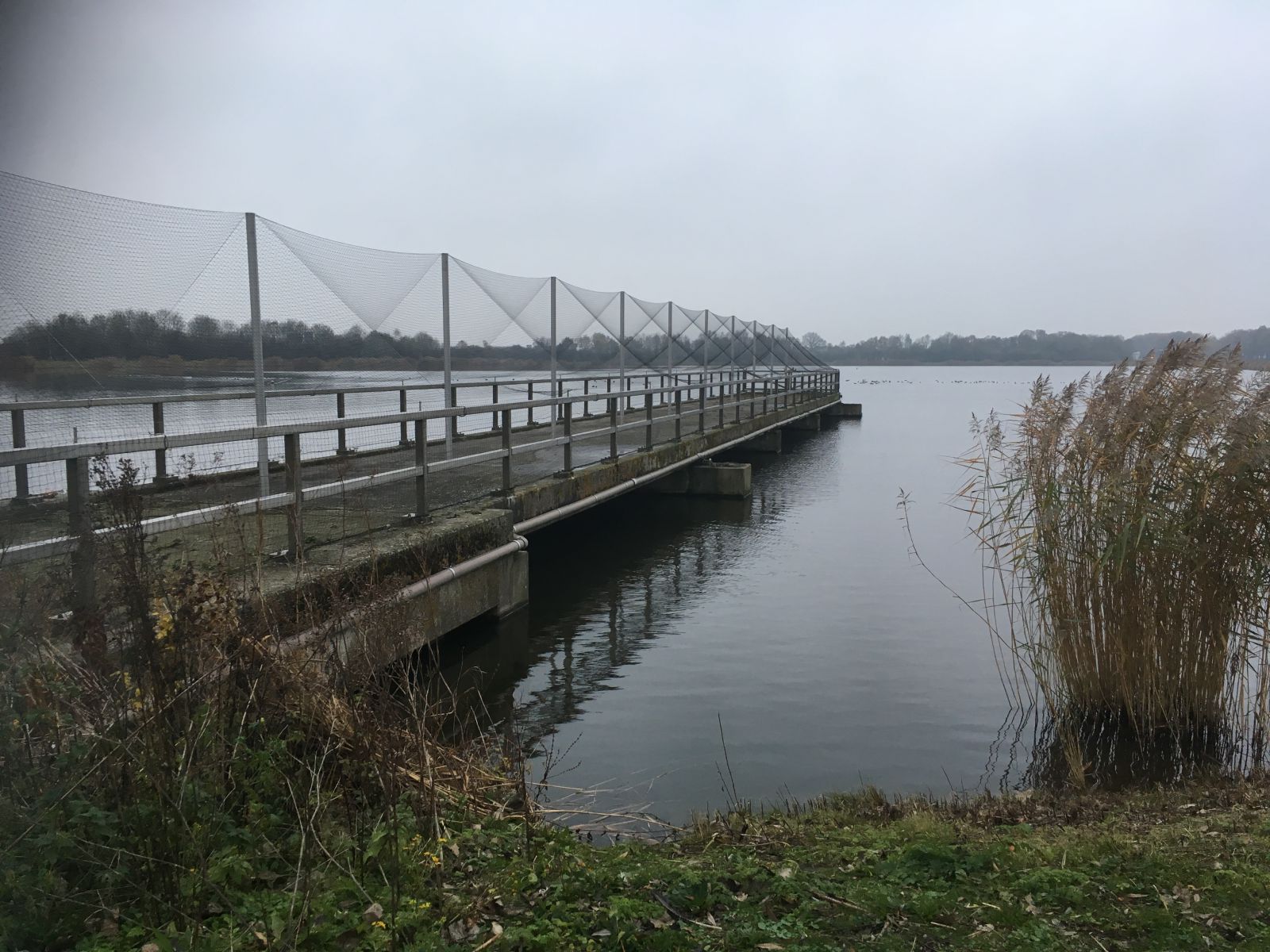
CFD modelling of the basins
We modelled the basin in 3D, realistically accounting for:
- Aeration (2 coarse bubble aerators in the basin - not all reservoirs have aeration)
- The real basin geometry
- The actual flow rates
The input needed to run the simulations was very limited.
We injected a 'virtual tracer' in the inlet (not injected in reality!) to clearly visualise dead zones and shortcircuiting.
Four 'what-if' scenarios were tested:
- Influent flow rate 440 m³/h, aeration off
- Influent flow rate 440 m³/h, aeration on
- Influent flow rate 880 m³/h, aeration off
- Influent flow rate 880 m³/h, aeration on
Major findings
- As shown in the below figures, the impact of aeration was significant. Without aeration, the mixing performance of the basin was very poor (Figures 1 and 2).
- The strong coloured stream in Figure 1 indicates the influent, shortcircuiting strongly without aeration.
- A quantitaive comparison of the mixing in all cases is shown by the Rehman-Nopens curves in Figure 3. The steep curves (more homogeneous system) show good mixing in the case of aeration.
- The impact of ifluent flow rate was limited in this basin. A higher flow rate led to slightly better mixing.
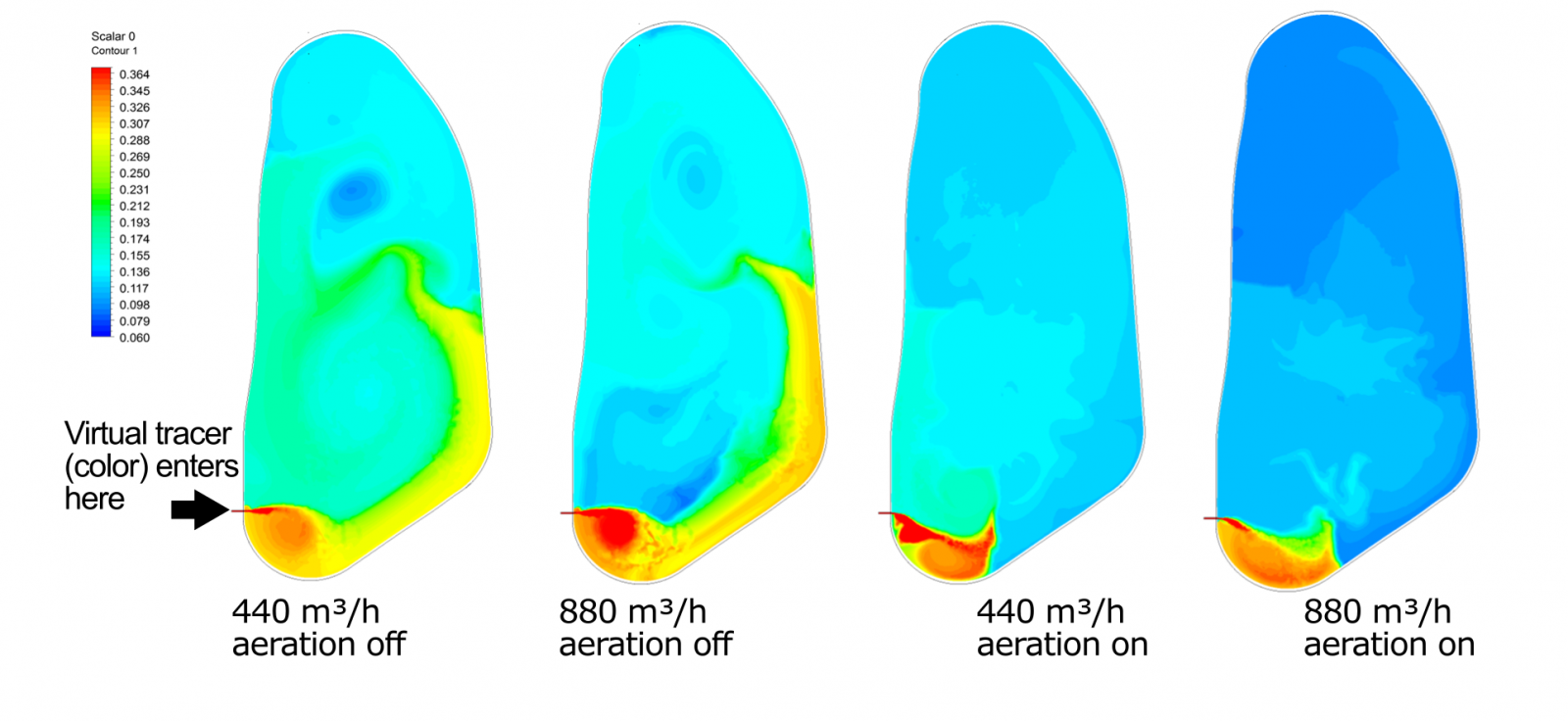
Figure 1: Comparison of 4 operational scenarios. Top view of the basin showing how the incoming flow (red/orange) is transported and diluted through the basin.
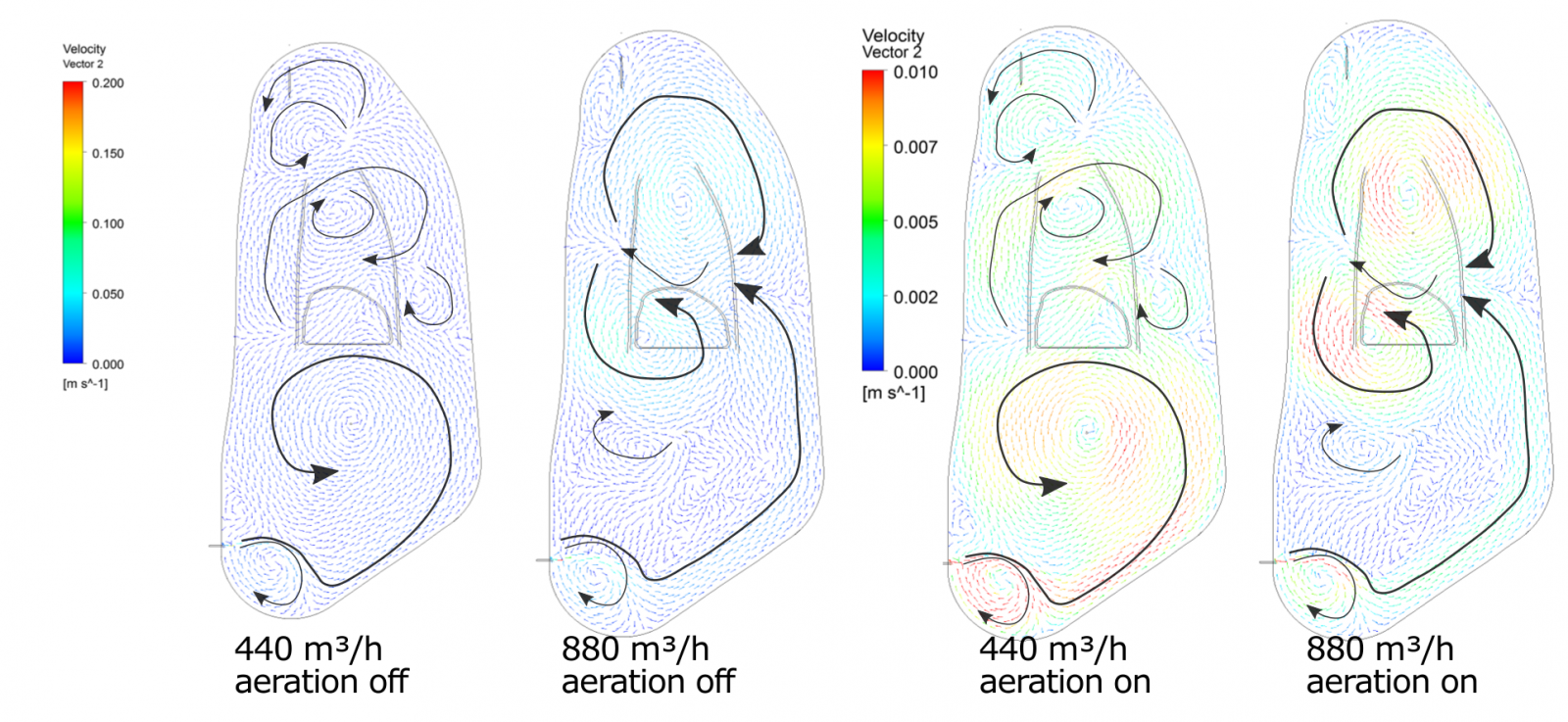
Figure 2: Comparison of 4 operational scenarios. Top view of the basin showing the major flow currents in the basin. Strong shortcircuiting is present when aeration is off.
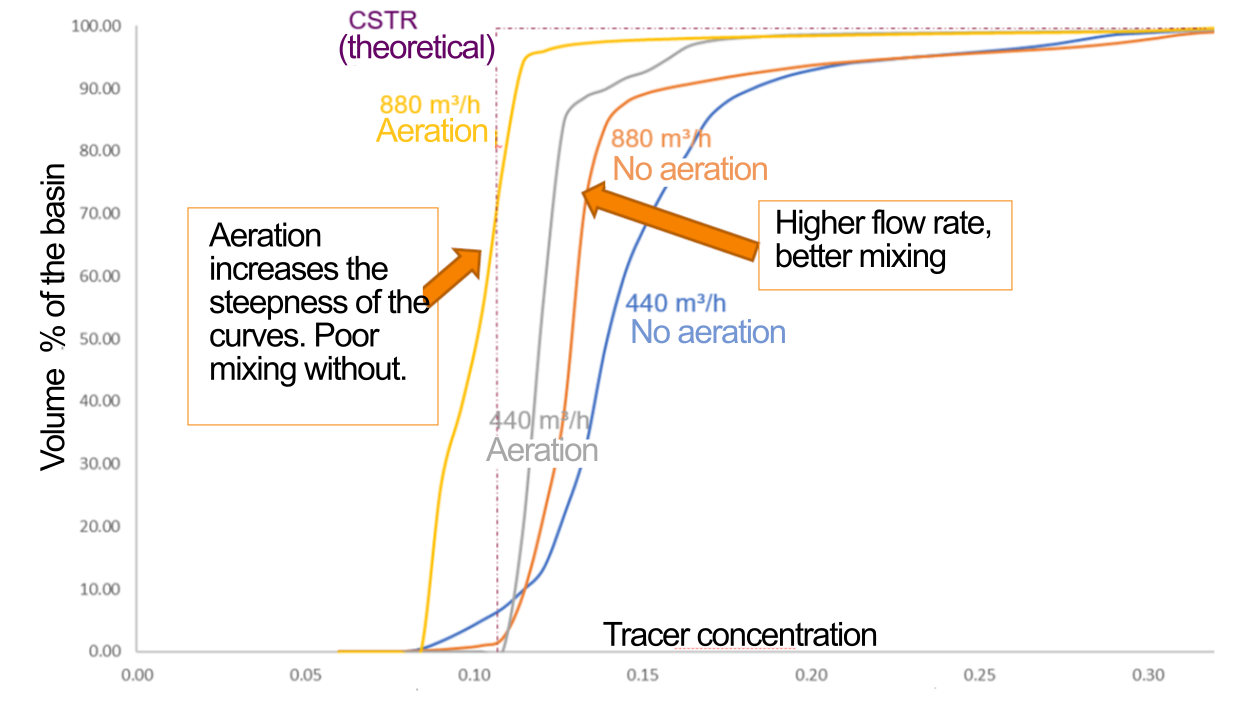
Figure 3: Rehman-Nopens curves quantitatively comparing each of the scenarios. The very steep curves indicate intensive mixing, while a sloped curve indicates dead zones and shortcircuiting.
Final impact of the study
- Aeration was switched off in winter. We recommended to have also limited aeration in wintertime, as mixing without aeration is extremely poor.
- Energy could be saved by reducing the aeration rates
- An alternative sampling location was chosen, as samples were initially taken in the 'shortcircuiting zone', where the water quality was not representative
Major conclusion
In a matter of a few weeks, new or existing basins can be completely analysed and design and operational improvements can be tested with the computer model before real implementation. This can lead to major improvements of performance and cost savings (incl. CapEx).
Suggested Projects
Subscribe to our newsletter
