The Deammonification (DEMON®) system upgrade for DC Water
AM-Team collaborated with DC Water to optimize their DEMON® system upgrade using advanced bioreactor CFD modeling. Through model-based design iterations, sensitivity of system performance to subtle design changes was revealed, ensuring compatibility with existing HYPERCLASSIC® mixers. The new system now reliably meets effluent quality targets, with the entire simulation project completed in just six weeks.
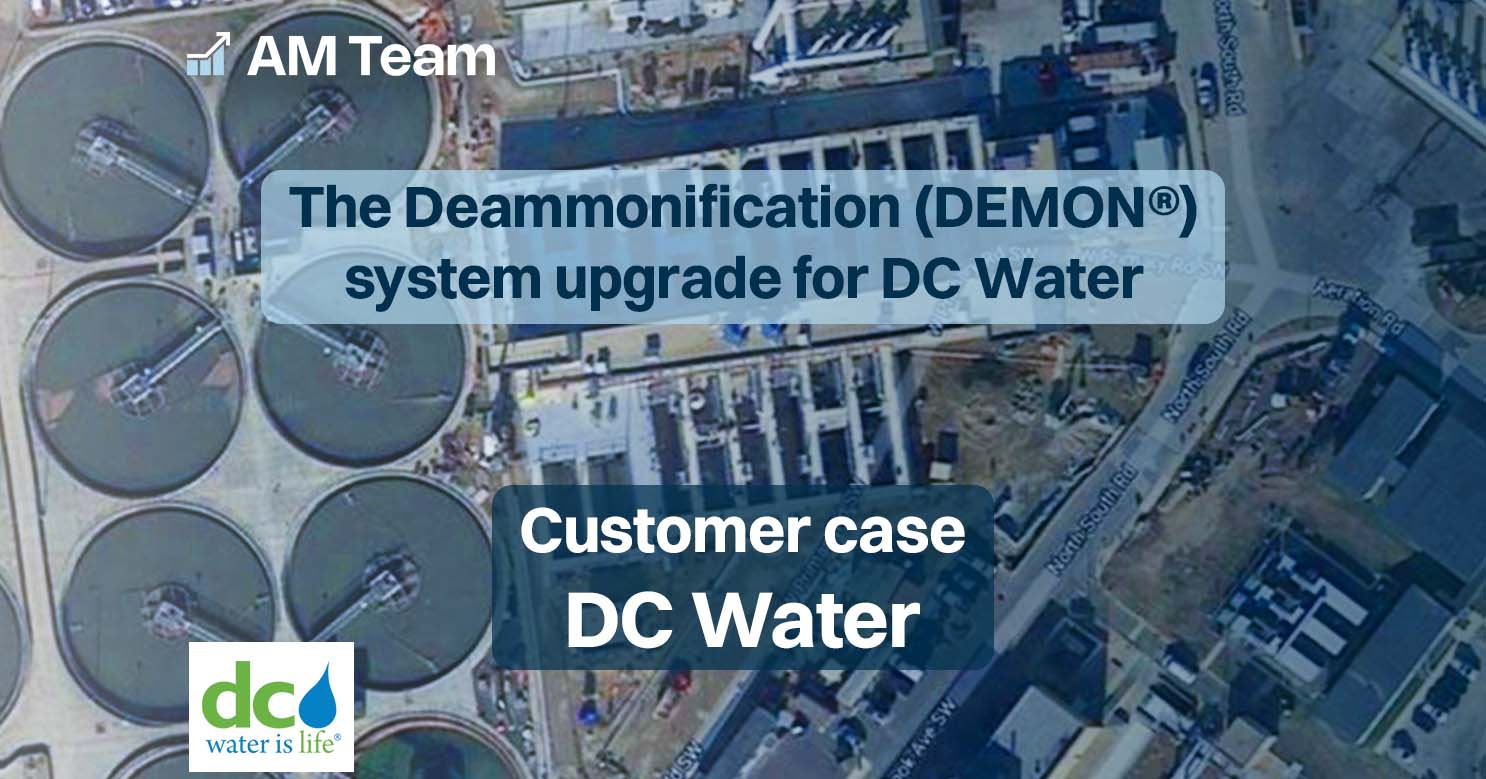
Case highlights
- AM-Team’s bioreactor CFD model was used to support DC Water’s DEMON® system upgrade
- Specific flow patterns were identified that needed to be considered during redesign
- The DEMON® baffle system was made compatible with the existing HYPERCLASSIC® mixers
- Model-based design iteration revealed the sensitivity of system performance to subtle design changes
- The new system was installed and is operating as expected, reaching the desired effluent quality
- Simulation project turnaround: 6 weeks
Introduction and Problem statement
DC Water (Washington D.C., US) operates world’s largest advanced wastewater treatment plant: Blue Plains. The plant has installed a unique array of advanced treatment technologies for wastewater treatment and resource recovery. One of those technologies is the deammonification (DEMON®) process, an anammox-based process removing nitrogen from concentrated side streams.
The original installation consisted of six sequencing batch reactors (SBRs) (Figure 1), but mechanical issues and success of other continuous feed installations led to consideration of a baffle wall configuration. This integrated clarifier structure could both mitigate operational issues and enable continuous operation.
However, proper implementation of the baffle wall prior to construction was identified as critical. The baffle wall (developed by Dr. Bernhard Wett) had been successfully installed in other DEMON® systems but had not been used in combination with a HYPERCLASSIC® mixing and aeration system. Solids settling needed to be evaluated within the baffle under all circumstances. Fixing suboptimal performance would be very difficult once installed. That is where a model-based assessment came in.
Solution and objectives
DC Water and Dr. Bernhard Wett (inventor of the DEMON® process; ARAconsult) worked with AM-Team to conduct Computational Fluid Dynamics (CFD) modelling. CFD is based on established physics and allows 3D assessment of existing or new designs.
The objectives of this project were to:
- investigate the flow patterns caused by the mixers in the initial design, in view of optimal baffle integration and associated risks on short-circuiting
- optimally integrate the baffle system in DC Water’s specific highly turbulent reactors, avoiding air entrance in the baffle while stimulating solids settling. Different designs would be virtually evaluated and compared as needed.
“The CFD simulations of AM-Team provided us with confidence that the baffle system would work in combination with the specific mixers and reactor configuration we had. It was spectacular to see how realistically CFD accounted for our equipment and the mixture of water, solids and gas. Subtle design changes made a big difference.” - Shawna Martinelli, Director of operations and process engineering, DC Water
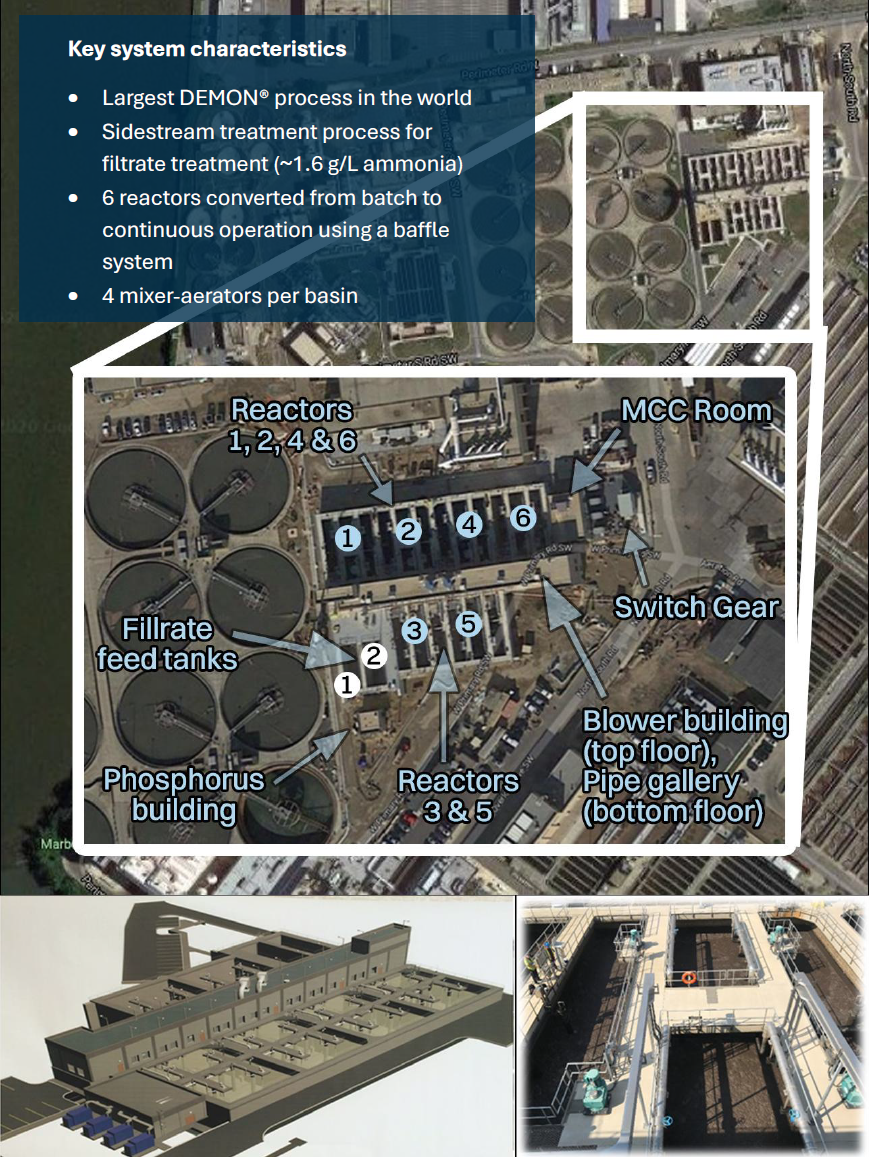
Approach
AM-Team’s tailored bioreactor CFD model was used to simulate the system in full 3D. The model accounted for both the water and air (2-phase) and has dedicated functions to account for activated sludge or a mixture of activated sludge and Anammox granules in this case (i.e. these systems do not have to be simulated assuming ‘clean water’). The real system geometry (Figure 2) and even the rotation of the mixer/aerators could be easily taken into account with AM-Team’s approach.
Water velocities, turbulence and air distribution were visualized in critical areas of the system, and the existing and various new designs were assessed and compared to make an optimal choice.
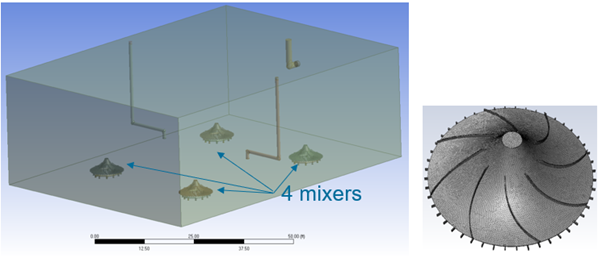
“As a system designer, I have worked with AM-Team several times to accelerate decision making and maximize system performance. The virtual ‘what-if’ testing functionality CFD can provide is of tremendous value during design.” - Bernhard Wett, founder at ARAconsult
Results and findings
Analysis of the original system
The simulation of the original SBR design revealed that the mixers were pushing the water over the bottom to the sides of the reactor, after which the water flowed upwards prior to recirculating to the middle (Figure 3). This information was important to consider in view of baffle integration, as the upward flow could potentially disturb solids settling if not properly mitigated. The impact of aeration on the hydrodynamics was taken into account in the model.
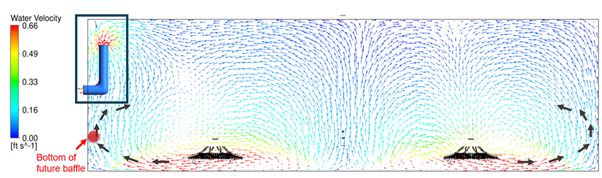
Virtual testing and selection of the new design
The concept of the DEMON® baffle wall, as proposed by Dr. Wett is shown in Figure 4a. Water, Annamox granules and sludge were expected to enter the baffle, while air bubbles were expected to stay at the outside of the baffle, gradually rising up alongside the baffle wall. The sludge was expected to settle in between the two baffle plates and flow back into the tank (indicated by the green arrows). A potential risk identified from the initial CFD analysis (see above) was the high flow over the bottom and the sides of the reactor induced by the hyperbolic mixers. To prevent air entrance induced by these forces and short circuiting of sludge and Annamox granules, a deflector was hence to be installed at the bottom of the baffle wall.
“In a matter of weeks, we could determine design modifications with our project partners. Model-supported design provided us the necessary confidence for full-scale implementation. The process modification turned out to be very successful, with excellent solids separation and effluent quality in a continuously operating system.” - Shawna Martinelli, Director of operations and process engineering, DC Water
CFD revealed the importance of proper hydrodynamic design and the sensitivity of the system performance to subtle design changes. Even though the initial deflector was rather large (Figure 4b), the simulation identified an undesired flow pattern leading to air entrance in the settling zone (Figure 5a), potentially causing solids washout. Consequent design iterations using the CFD model resulted in an optimal design that was expected to lead to optimal flow patterns outside the baffle (Figure 4c) and avoidance of air inside the baffle (Figure 5b).
Upon finishing the 6 weeks simulation/design project, implementation could start. DC Water replaced floating decanters with effluent weirs inside the the baffle wall. This successfully turned the DEMON® reactors into fully continuous processes.
As shown in Figure 6, an air-free settling zone could be obtained, allowing proper settling of Annamox granules and clearer effluent.
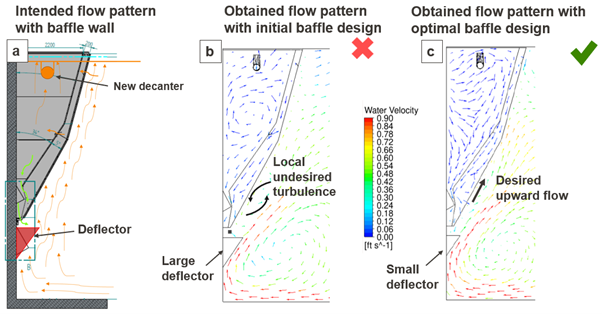
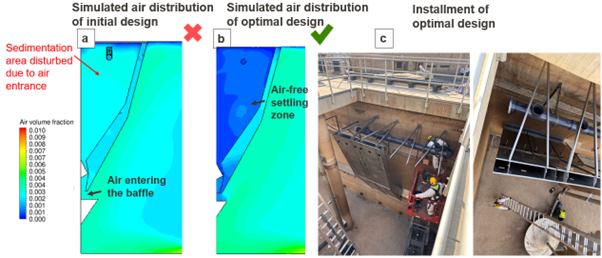
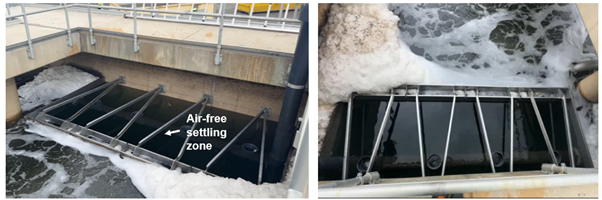
“Our industry often is surprised about the capabilities, speed and practicality of today’s CFD models. We can easily account for the typical mixtures of water, solids and gas that are omnipresent in water treatment and can even include chemical or biochemical reactions. These capabilities offer unprecedented design power.” - Simon Duchi, Senior simulation engineer and project manager, AM-Team
Conclusion and impact
DC Water could improve reactor performance and convert the discontinuous SBRs into continuous DEMON® systems. The CFD simulations provided comfort in the location of the defector plate and combination of HYPERCLASSIC® mixers and baffle wall installation which was validated by a 6 month performance test of the application before converting all six reactors to continuous flow through. The CFD also accelerated the troubleshooting and problem solving prior to field installation. Based on solid physics, the CFD model could identify important flow patterns in the initial design and be used to iterate and optimize baffle implementation.
The new system is operating as expected, reaching the desired settling performance and resulting effluent quality.
Acknowledgements
We thank the project partners, specifically Shawna Martinelli (Director of operations and process engineering, DC Water) and Bernhard Wett (Founder, ARAconsult) for the great collaboration and their help in compiling this case article.
Suggested Projects
Subscribe to our newsletter
