The Ozonation Series – episode 4: Four factors that drive ozonation process performance and cost
Which elements have a significant impact on the performance and cost of your ozonation process? You can divide them into four big groups. Firstly, the water matrix has a considerable influence. Secondly, the human factor – the operator running the whole process – plays a role. Thirdly, the operational parameters of how you run your process are essential. And lastly, the design of your system. This blog drills deeper down on the last two.
Focus on what you can control
When you look at your ozonation process and the drivers behind its performance, many different elements impact your ozonation process performance and cost. The visual below gives you an overview. You can control just two groups of those: the process parameters and your equipment and system's design.
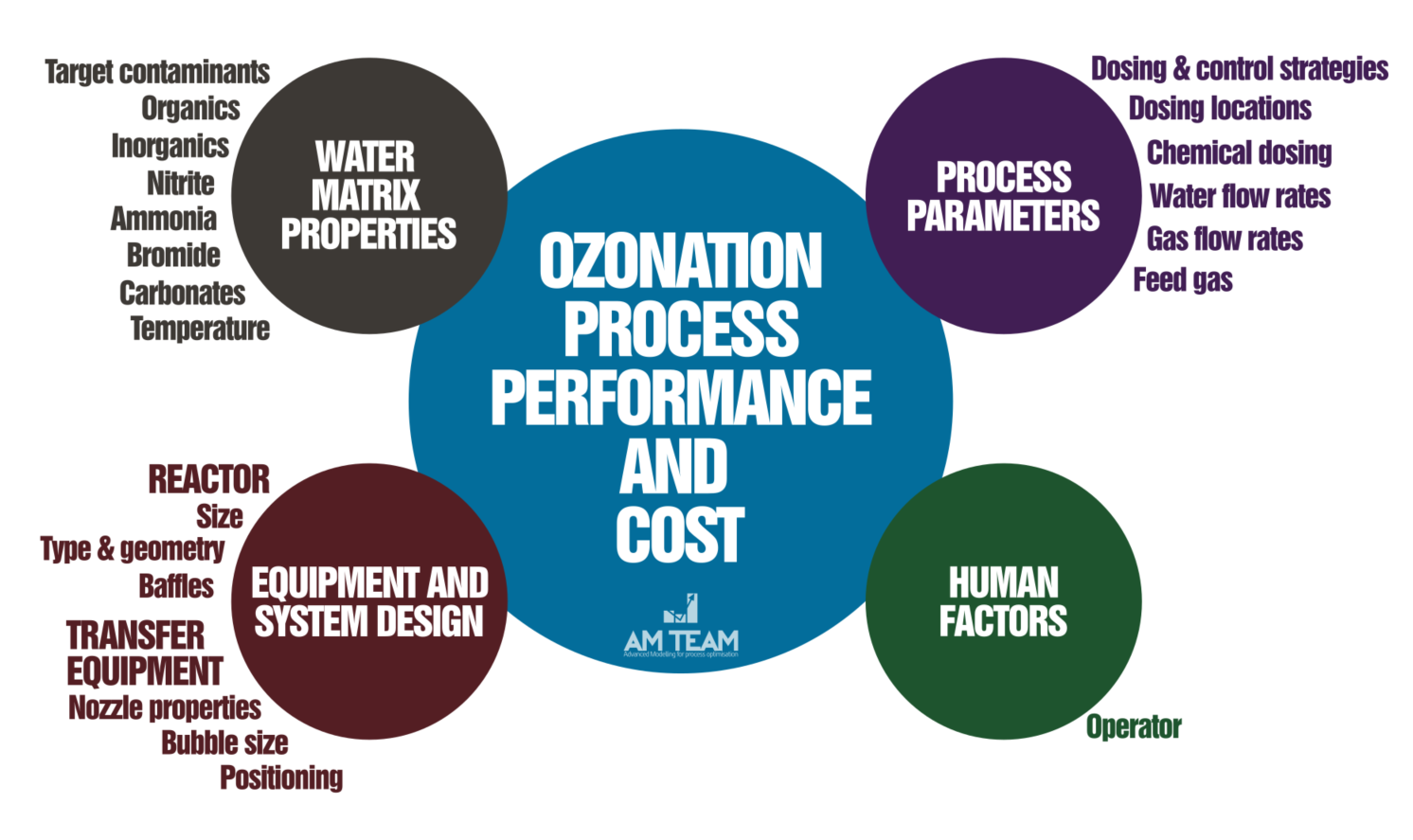
The process parameters are operational factors like your dosing and control strategy, water and gas flow rates, the location of your dosing etc.
How you design your plant and your reactor and transfer equipment is your decision. You select the reactor type, its size, and the baffles' positioning. When it comes to your transfer equipment, you also have a couple of design options: how does your nozzle look? What's the bubble size? Where do you position your transfer equipment?
Watch the video to see how your choices in process parameters and equipment and system design matter.
Designed for operational excellence
How your plant performs largely depends on the design choices you made initially and the specific composition of the water matrix. With Computational Fluid Dynamics (CFD),coupled with kinetics simulations, you get insights on the decisions you need to make in the design phase to run your ozonation process more efficiently and match the performance better with the specific water matrix at your plant. By understanding your process better, you can make decisions easier and faster and eventually save costs.
You can impact a lot during the design phase. Sizing, for instance: can the reactor be smaller to make it more efficient? You can look at the detailed design: where do you put baffles? How can you reduce bromate? Where should you add peroxide? How can you improve ozone dissolution?
Next to the design of your reactor, you can also look at improving the design of your transfer equipment like the pipeline flash reactor with a static mixer, looking at dissolved ozone going through, venturi pipes etc.
Conclusion
Many different elements impact your ozonation process performance and cost. Process parameters, equipment, and system design choices significantly impact the efficiency of your final ozonation process. Virtual simulations allow you to get the right insights to make smart choices for the future.
Discover the ins and outs of ozonation
Read our ozonation blogs if you’re interested in ozonation for water treatment. Happy reading!
Subscribe to our newsletter
