The power of virtual piloting for faster and more effective scale up
Scale-up of a new technology is challenging. Besides expertise, it needs persistence and significant amounts of time and money. Talking to a lot of water technologists worldwide, these factors matter and often play out simultaneously. This post is about the potential of advanced 3D process models* for accelerated and more reliable scale-up. This so-called model-based design is still largely untapped.
*We use this terminology for the next generation computational fluid dynamics (CFD) models that include process phenomena such as kinetics, particles and others solids, bubbles etc.
The scale-up of new technologies
Major drivers for technological innovation are more stringent regulatory requirements, the trend towards resource recovery (incl. water reuse),population growth and other challenges (e.g. micropollutants and climate change).
Technologies must do more with less space while being more reliable and efficient. And this in a world evolving faster than ever, where technologies become more complex and scale-up should deliver a working full-scale concept as fast as possible and preferably at lowest cost.
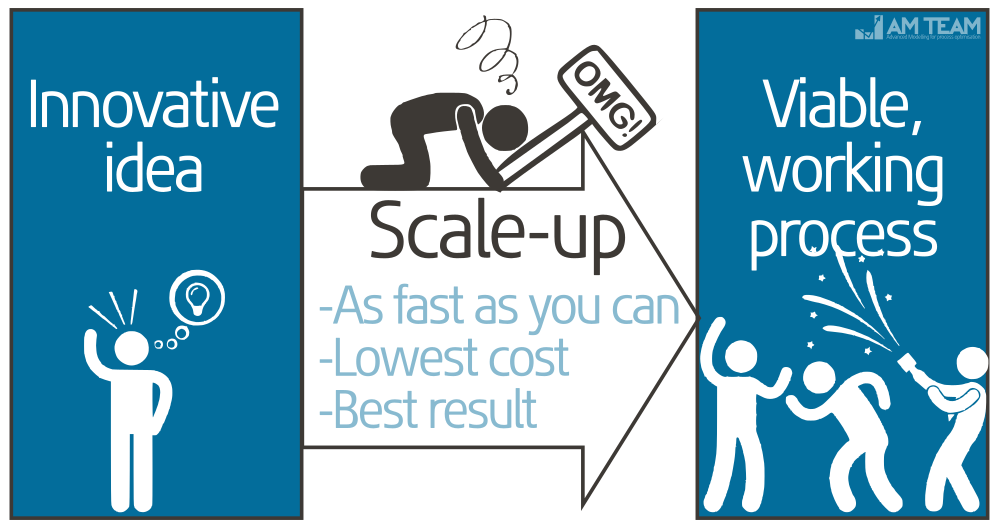
Scale-up would be a lot easier if everything, including the water molecules, would scale along with the reactor. Once I heard the following quote:
Raising children is much more complex than only buying them larger clothes
If you are a parent yourself, you will probably understand.
So the question is: can we accelerate scale-up while simultaneously lowering scale-up cost and effort and increasing performance and reliability of the final design? Combining the technological savvy of technologists with in- depth advanced 3D modelling expertise has huge potential in this respect. See it as any specialist relying on advanced equipment, such as surgean relying on special scanning devices to take decisions.
What is virtual piloting?
Virtual piloting has the following two goals:
- To reduce, replace or complement experimental trial and error with virtual experiments to save time, cost and effort
- To acquire new, high resolution information that leads to more insight, better performing technologies, lower safety factors and more confidence
If you have no or limited experience in using models that far, it probably sounds too good to be true. Of course! Experimental testing and measuring is and will remain of high value. We should just understand that today’s models can be highly accurate and powerful and that computers are faster than ever. The times in which one needed ‘multiple days’ for 1 simulation are over. And by the way, imagine a simulation would take several days. What’s the point in a scale-up exercise of several months to over a year?
CFD is too often used to confirm or double check an earlier made decision. It has value, but it is nothing compared to the concept discussed here, where advanced simulation influences decision making to some or to a large extent. The ratio real experimenting vs virtual experimenting can vary a lot throughout projects, but the value is very high.
What is the current status of the models?
Let’s look at typical process phenomena in a water or wastewater treatment system, where we can have bubbles, solids and liquids, sometimes reacting and interacting:
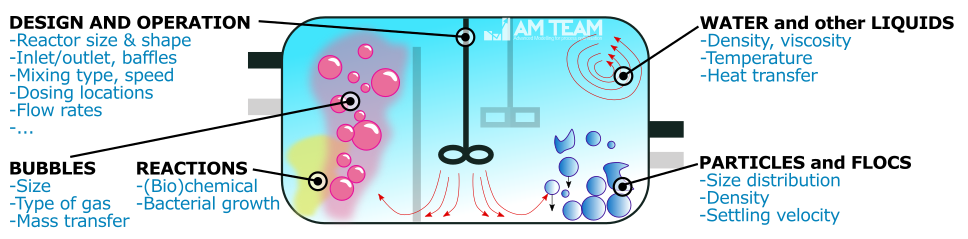
The technology designer’s role is to control these phenomena as good as possible in a well-designed treatment process. But as the figure shows, there are so many design and operational variables. To test all of them is practically infeasible, and one often has to make a smart selection of these. For example, we had a project in which the following factors determined the end result:
- Filling and emptying time and water levels (operational cycle)
- Aeration rate
- Bubble size
- Reactor shape
- Reactor dimensions
- Baffle height
- Number of inlets
- Inlet diameter
- We used a very realistic CFD model to go from the 3 m³ pilot to a 100 m³ full-scale performing equally well. The model included 2 different bubble sizes, mass transfer, kinetics and accounted for the system specific viscosity due to solids.
Example of a dynamic 3D simulation, including air, liquid and kinetics
This was a typical case where scale-up problems were not solved by only showing where the dead zones were. We needed to calculate the final water quality, in terms of concentration levels.
We have seen many examples in which pilot design was altered along the way (eg opening and replacing part of the reactor),consuming a lot of man hours and expensive reactor material. Many of those prototypes could have been tested virtually at a fraction of the cost.
One of our clients could cut the development time of a new technology by half, while saving a lot of stainless steel and man hours. The final “model-based” design exhibited excellent performance.
The earlier mentioned goals of virtual piloting are illustrated in the following pareto-plot: not only should you be able to accomplish more with 20% of the effort (efficiency and speed),the reachable maximum will be higher (more effective process).
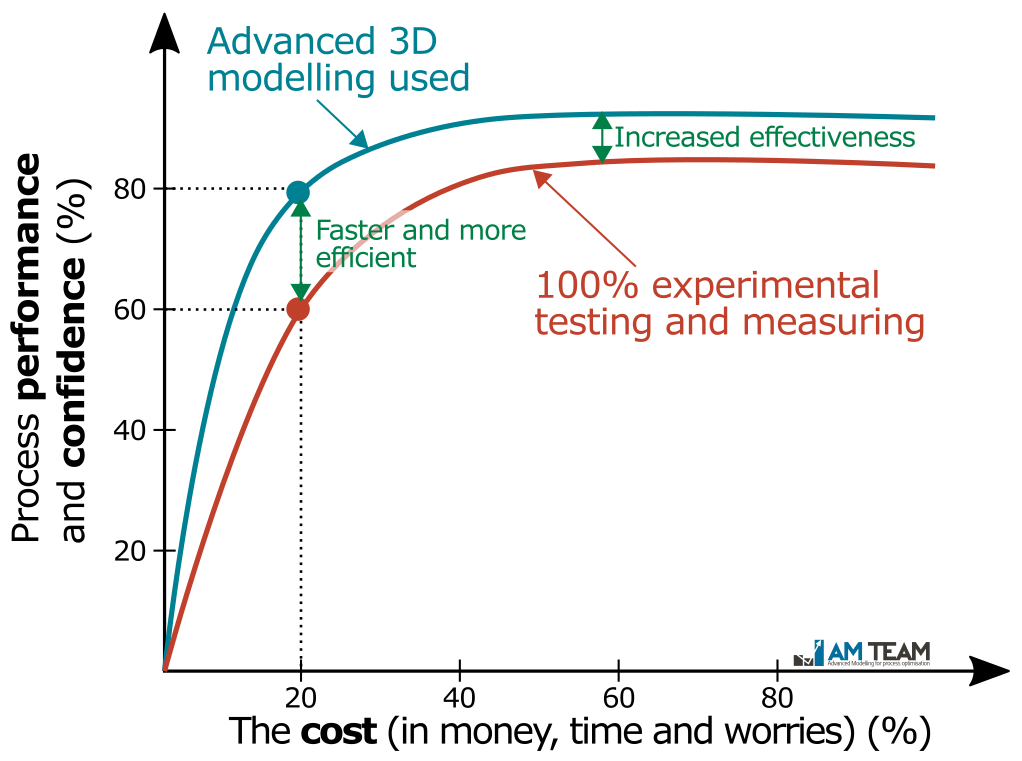
And what about validation?
We knew you were thinking about that! Let’s first make clear that CFD is based on physical principles, which means that proper application already leads to a decent default accuracy. This is also why CFD models typically need limited input to get started. However, when the stakes are high, which is often the case in scale-up projects, model validation has a lot of benefits and the relative effort is low. Scale-up means that at least a lab- or pilot scale system is available. There lies the opportunity to challenge the model. Typically, we validate the hydrodynamic part (using different measurements) and process part (e.g. by performing concentration profiling). After validation, the confidence in the model allows the virtual scale-up.
We recently performed a quite spectacular validation campaign at full-scale. Read the full blog post or watch the movie:
Conclusion
Experiments and models go hand in hand, just as technologists and advanced modellers have huge co-creation potential. The era of advanced computation is here. Let’s harvest its potential to speed up technology development and its full-scale implementation. Model-based design and virtual piloting are mature tools that are ready to disrupt the traditional rule of thumb scale-up.
Authors: Wim Audenaert, Usman Rehman, Ingmar Nopens
Stay informed
Watch our latest movies at AM-TV
Subscribe for the 'free information letter' (bottom of page)
Subscribe to our newsletter
