Make your pilots virtual: three ways how Computational Fluid Dynamics (CFD) simulation improves your process design and scale-up
Developing new water resource recovery (WRR) technologies takes significant amounts of time, cost, and effort. Years of extensive testing and piloting often precede mainstream market breakthroughs. Figure 1 below shows the technology lifecycle, from initial R&D to final application on-site. From a cost and operational perspective, CFD simulation can play a significant role in each of these application phases. This blog article focuses on the disruptive applications of CFD in the R&D stage: virtual prototyping and virtual piloting.
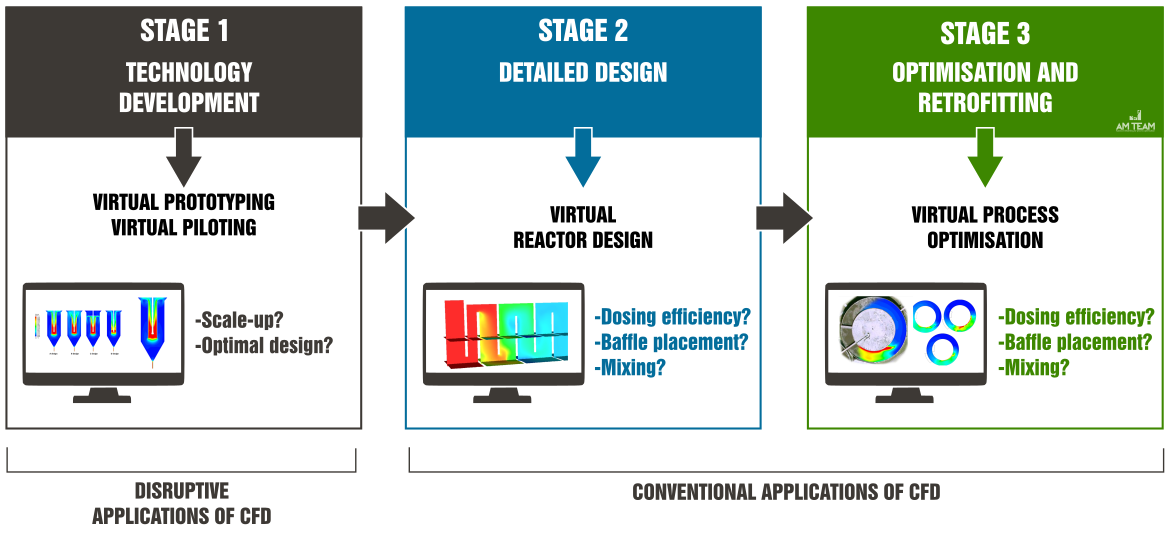
Figure 1: The treatment technology lifecycle – in each of the steps, CFD has specific applications
In the water industry, these applications often take the form of 'hydraulic checks' or 'mixing improvements', leading to better process performance and energy savings.
The three major benefits of using Computational Fluid Dynamics during technology development and scale-up
- Reduce testing costs and time
'Real-life testing' requires a significant investment in terms of resources, time, and budget in your design and development process. Testing and improving hydrodynamic factors at different scales can be assessed quicker and more accurately using advanced 3D CFD models. As you need fewer pilots, you further reduce the time and money you spend on testing.
- Speed up Time To Market
Developing a new technology or process takes time. Reducing or even entirely replacing physical pilot trials with virtual piloting leads to drastic cost and time savings and will minimize your time to market. In our fast-moving society, the window of opportunity to develop and launch a new technology is much smaller. That's why you need to move faster. With CFD, you can reduce your total Time To Market to just a couple of months rather than years.
- Acquire more in-depth knowledge
CFD opens up a whole new range of in-depth insights that you cannot acquire with real-life testing, allowing for disruptive process design. CFD models allow 'virtual prototyping' and 'virtual piloting' and simulation of variables that we can't measure in real life, such as concentrations gradients, shear distributions etc.
Additionally, by proactively integrating CFD in the technology development process, quality is built in from the start, which leads to 'Quality by Design' (QbD). You can apply in-depth insights you gained from the CFD simulations in your design process. And you avoid troubleshooting and optimization.
We'll further illustrate the capabilities of virtual piloting using CFD with two examples.
Case 1: The virtual scale-up of a novel baffled membrane bioreactor (BMBR) technology in Japan
Maezawa Industries, Inc. (Japan) is developing a BMBR technology. In stage 1 of their scale-up, they saved over a year of Time To Market and hundreds of thousands of euros of development cost. A validated advanced CFD model was used to scale up from a 3m³ operational pilot to a 100m³ large-scale installation (Figure 2).
We changed operational and design factors in different virtual designs (e.g. operational cycle settings, baffle design). In addition, we visualized mixing and local concentrations of nutrients, COD, and dissolved oxygen via 2-phase simulation (water and simultaneous coarse and fine bubble aeration) with integrated biokinetics (ASM1) and a sludge density function (Rehman, 2016). The large-scale installation successfully started operating in 2021.
> Watch the customer testimonial video to discover how Maezawa benefited from CFD modelling
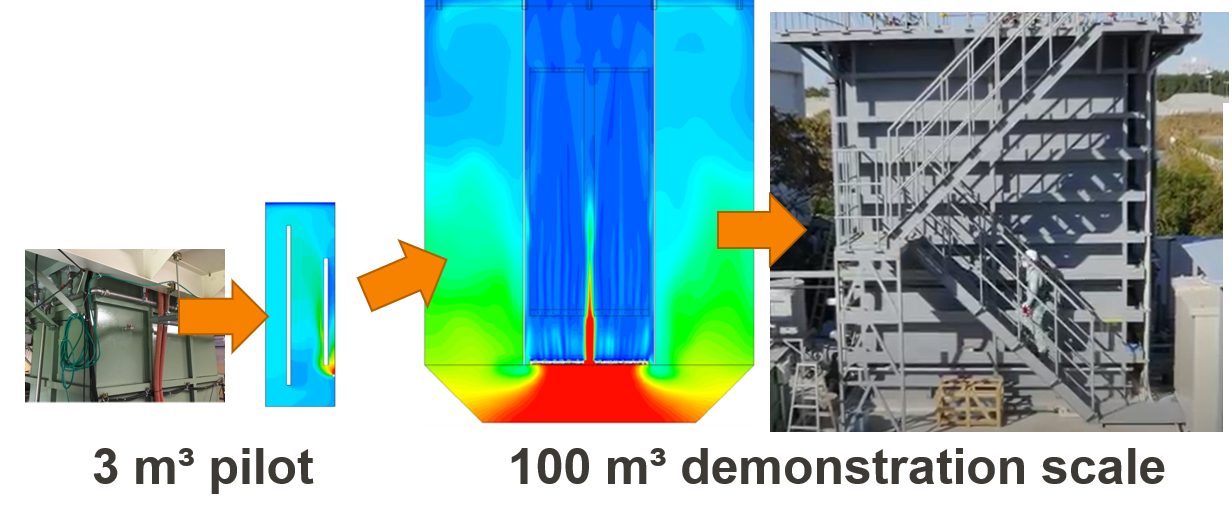
Figure 2: The virtual piloting process for the BMBR – we virtually tested multiple full-scale designs before construction. Maezawa industries built the best performing design and successfully started operation in Tokyo (Japan) (picture on the right)
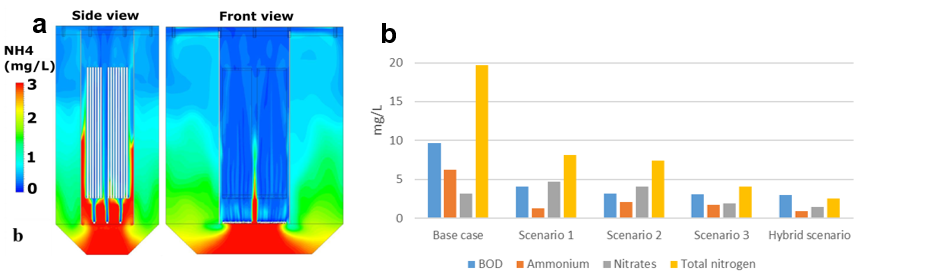
Figure 3: Different view planes of the ammonia gradient inside the large-scale BMBR (side view and front view) (left) and permeate quality for four different large-scale candidate designs (right)
Case 2: The virtual prototyping of novel tubular ultrafiltration (UF) membrane technology
CFD modelling is also suited for membrane design. Different shapes or properties of membranes can be virtually tested in detail. This is what we call 'virtual prototyping'. As opposed to the first case, which relates to virtual piloting for scale-up, this case relates to 'virtual prototyping' (i.e. virtual alteration of designs within a certain scale).
Pentair developed 'twisted' membranes by introducing a helical ridge inside tubular ultrafiltration membranes to promote turbulence through a helical flow. We modelled the flow inside the tubular membrane in high resolution using a single-phase CFD model (i.e. 'water only'). The shear stress on the membrane surface was quantified by CFD, as elaboratively described in Naessens et al. (2019). In addition, we compared the traditional tubular membrane design to the helix-shaped structure (Figure 4).
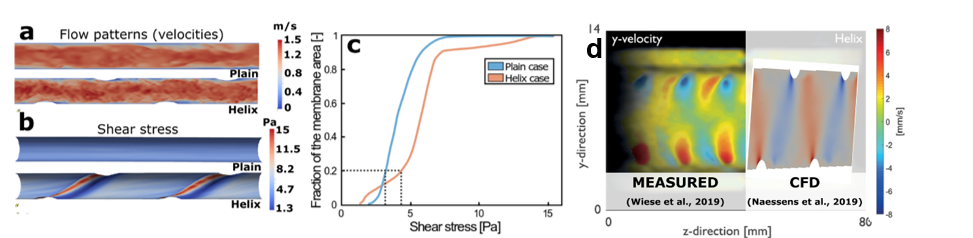
Figure 4: Compared to the plain tubular membrane, the helical ridges lead to high turbulence (a) and local shear (b). The comparative Rehman-Nopens curves (c) clearly show the shift to the right. Measured (left) and simulated (right) velocities inside the tubular helical membrane show excellent qualitative validation (d).
> Continue reading about this case in our blog on CFD for membranes
Conclusion
The two examples illustrate the power of CFD for accelerated process design, development, and scale-up. You can save time and money while learning more about your process, thanks to virtual prototyping and virtual piloting. CFD applications span a whole spectrum of technologies, including biological, electrochemical, physical, physical/chemical and chemical treatment technologies.
References
- Audenaert, W., Bellandi, G., Pearce, R., Takács, I., Buehlmann, P., Hogard, S., Salazar-Benitez, G., Jourdan, N., et al. (2019) Compartmental Modelling in chemical engineering: A critical review. Chem. Eng. Sci., 210, 115196-115215
- Naessens, W., et al. (2018) Impact of a Helical Ridge within a Tubular Membrane Channel on Fluid Flow and Particle Behavior: A Model-Based Analysis. Ind. Eng. Chem. Res., 57, 15586−15596
- Nopens, I. et al. (2020) Water and wastewater CFD and validation: are we losing the balance? Wat. Sci. Tech., 81(8),1636-1645
- Rehman, U., et al. (2017) How well-mixed is well mixed? Hydrodynamic-biokinetic model integration in an aerated tank of a full-scale water WRRF. Wat. Sci. Tech., 76(7-8),1950-65
- Wett, B., et al. (2014) Operational and structural A-stage improvements for high-rate carbon removal. IWA Specialist Conference on Sustainable WWT and RR, Kathmandu, Nepal
- Wiese, M., et al. (2019) Fouling minimization at membranes having a 3D surface topology with microgels as soft model colloids. J. Mem. Sci., 569, 7–16
Subscribe to our newsletter
