Optimal pure oxygen mixing and transfer
Computational fluid dynamics (CFD) was used to optimise mixing and pure oxygen transfer in industrial wastewater treatment. Two pure oxygen injectors were supplied by Air Liquide (Ventoxal). Dead zones cured and optimal mixing obtained.
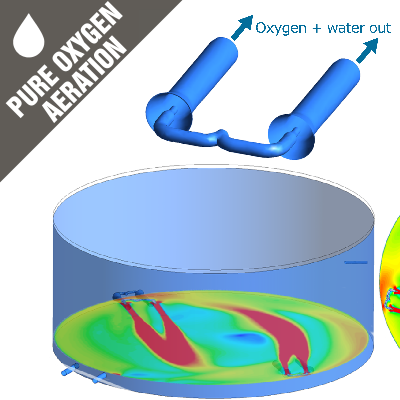
The questions we answered
Pure oxygen as an aeration technology for wastewater treatment is rapidly growing due to multiple benefits such as smaller footprint and cost saving. Optimal oxygen transfer is key. Our client Air Liquide was installing its propriatary Ventoxal technology in a new bioreactor. The Ventoxal technology combines two roles: mixing and oxygen introduction. We used 2-phase CFD + biokinetics to answer the following questions:
- How to mix the bioreactor optimally for efficient influent mixing while
- Obtaining optimal oxygen distribution?
We modelled the system in 3D and virtually tested four different designs in a couple of weeks. The best scenario was implemented at the plant.
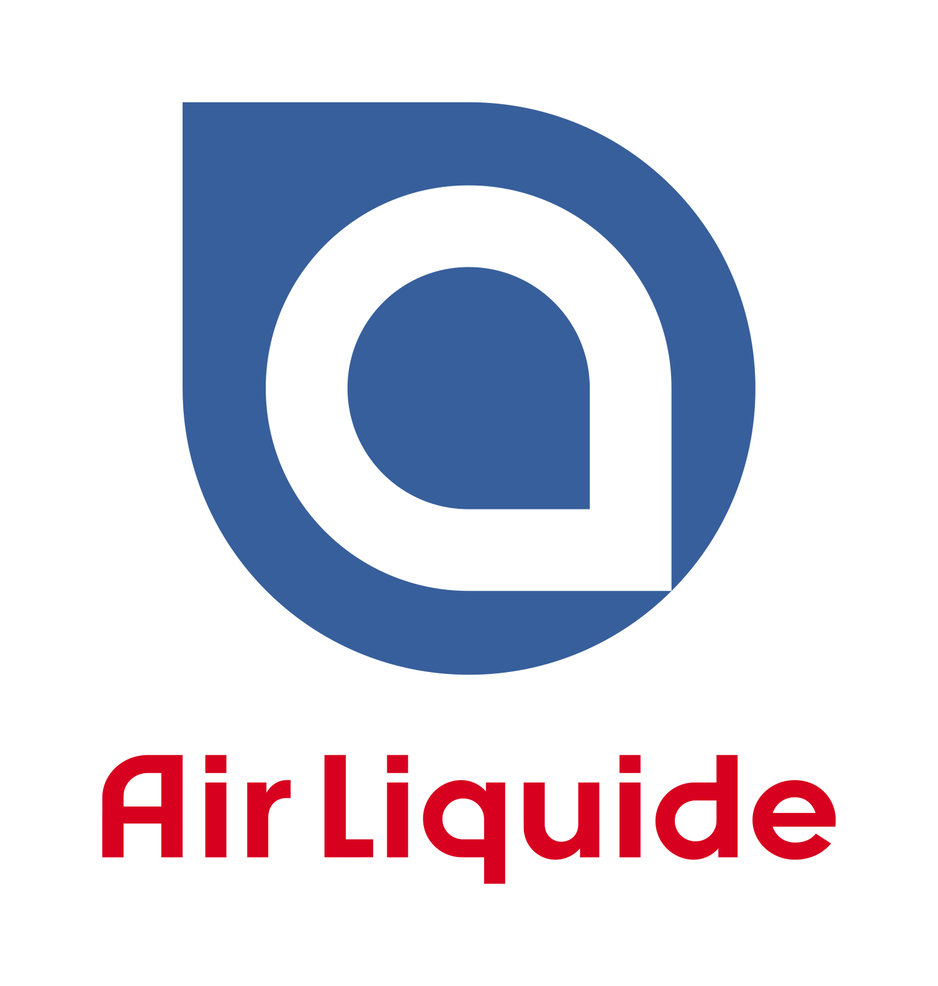
CFD modelling of oxygen mixing and transfer
We modelled the bioreactor, realistically accounting for:
- High speed injection of a pure oxygen/water mixture (water and gas phase)
- Oxygen transfer and oxygen uptake
- The reactor specific geometry and placement of Ventoxals (distance from walls and angle)
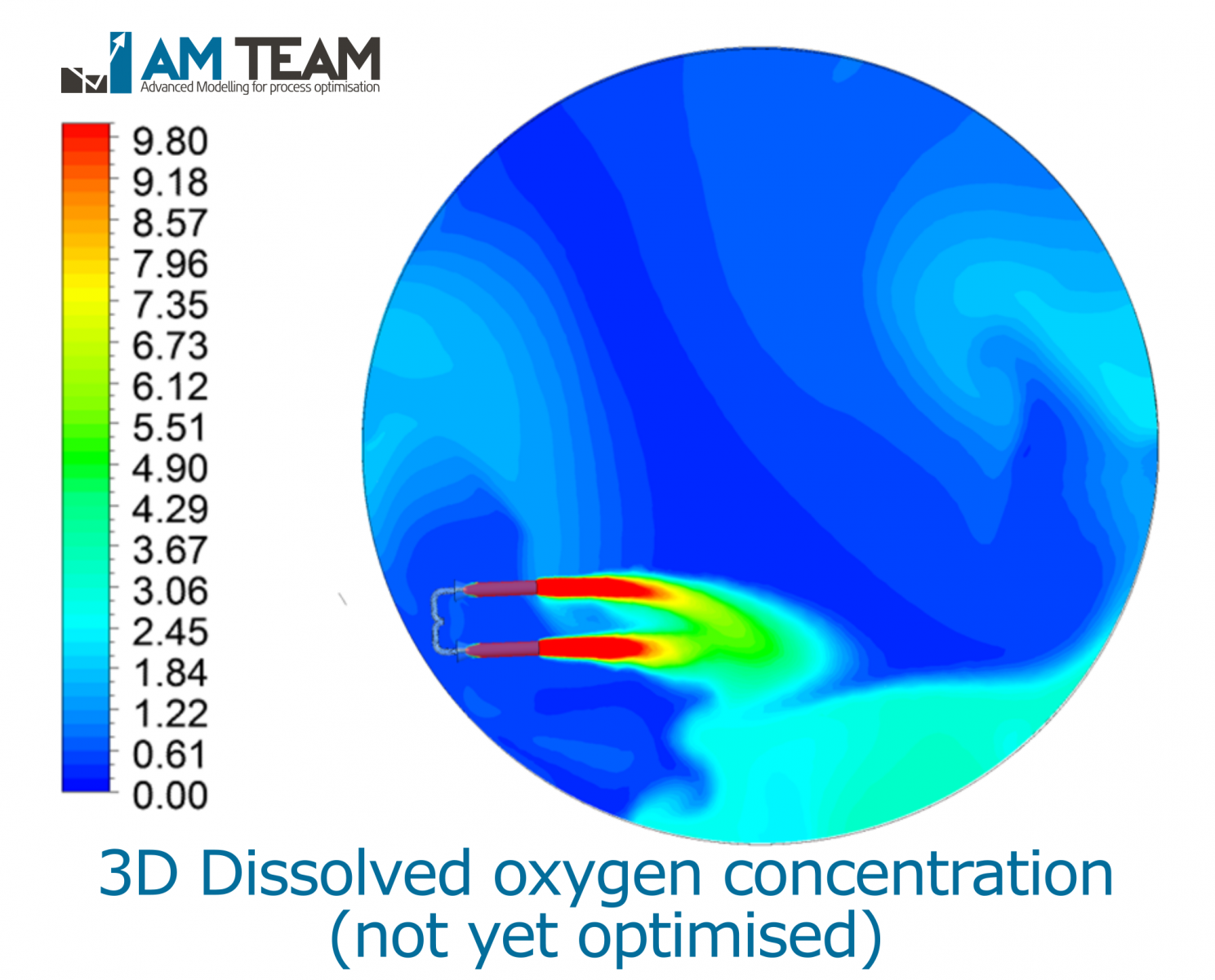
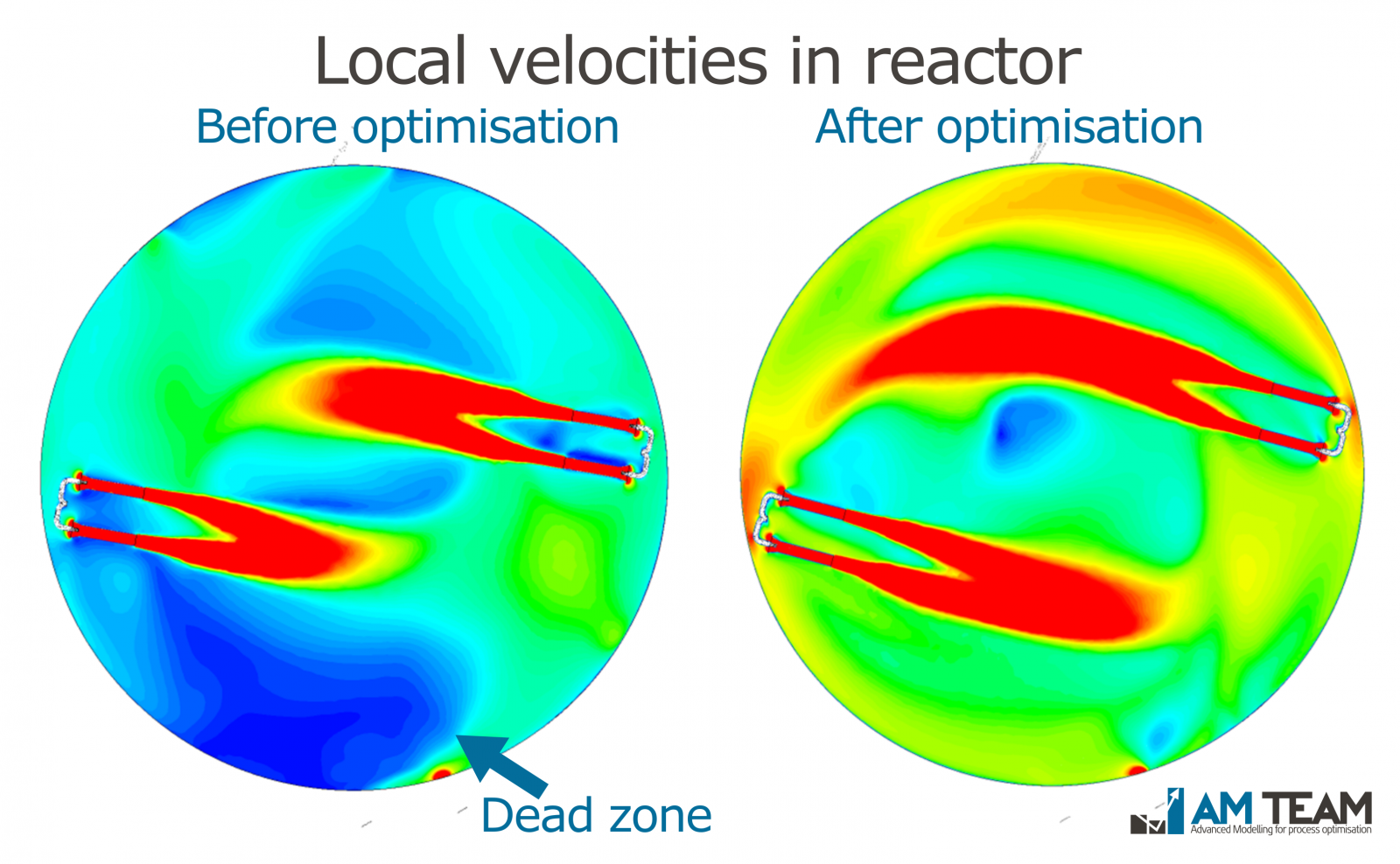
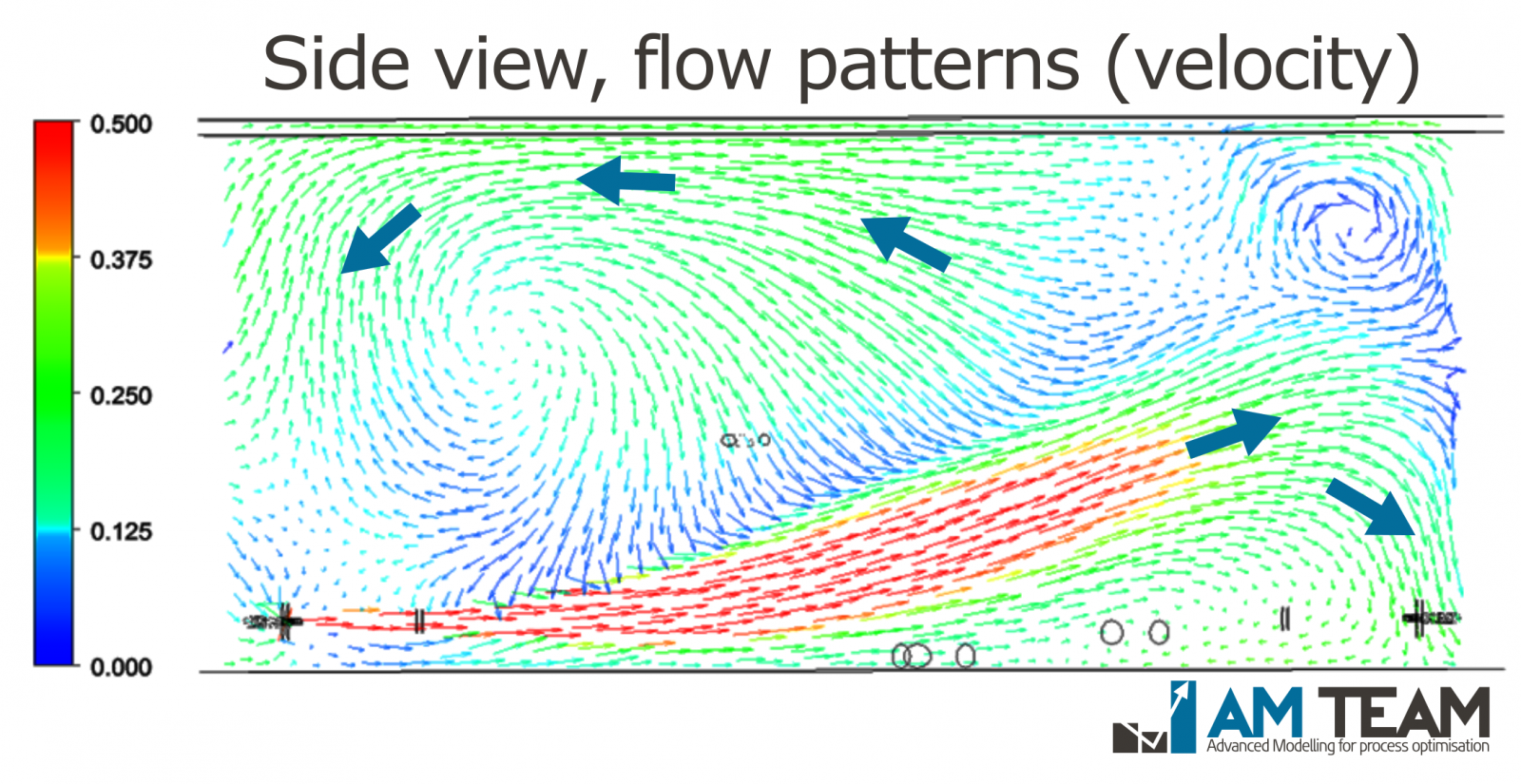
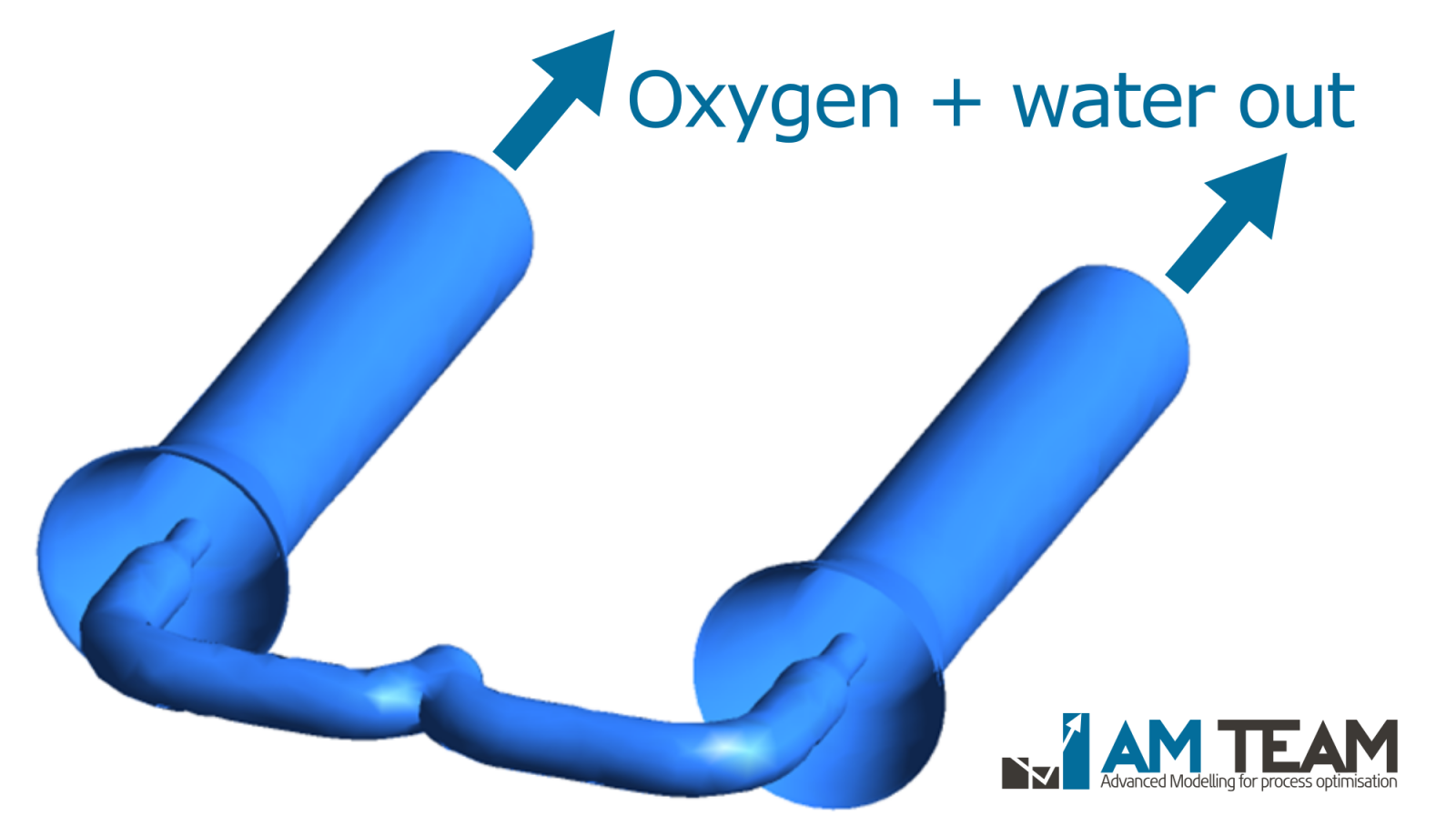
We injected a virtual tracer and the CFD model visualised dead zones and shortcircuiting and oxygen distribution. Different scenarios were run with different flow conditions, aeration capacities and oxygen introduction locations.The figure below compares three different scenarios on one easy to read graph. These so-called Rehman-Nopens curves summarize 3D CFD results on clear 2D graphs for easy comparison of different designs. The superior design had no dead zones and optimal synergy between the installed units, inlets and outlets.
Suggested Projects
Subscribe to our newsletter
